Designed for growth: Food waste is perfect for bio-gas generation
With the completion and commissioning of the Malchin food waste fermentation plant, its designer Entec Biogas GmbH of Austria, has obtained a further large-scale contract in this field of bio-gas technology. Planning is currently underway for the Selby food waste fermentation bio-gas plant in England; the first stage of construction is slated to begin this year.
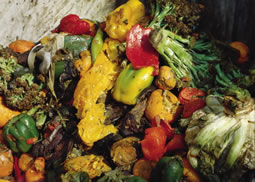
(01.06.2010) Bio-gas technology in connection with food waste disposal is increasing in world-wide importance. The increased global importance of this technology has developed against a backdrop of hygiene and disease prevention on the one hand, and economic and environmental concerns on the other. A serious foot-in-mouth disease outbreak in Great Britain, as well as the appearance of BSE, have resulted in prohibitions against processing animal waste into feed. From the economic perspective, it makes more sense to produce energy and high quality organic fertilizer based on nitrogen, phosphorus, and potassium (NPK fertilizer) than to use costly concentration and incineration technologies or problematic landfill techniques. Now a British group of investors is planning to build a biogas plant for food waste in Selby, England. After visiting a number of plants built by various companies, including the plant in Malchin (eastern Germany), the investors decided in favor of the planners of the Malchin plant, Entec Biogas of Fussach, Austria, to provide the technology.
The future plant will consist - depending on actual requirements - of two to three parallel processing lines, each with 2 MWel capacity and will be built on the site of an abandoned citric acid production plant. Unlike the plant in Malchin, which generally processes only liquid or slurry-type wastes delivered in trucks, the Selby facility will use a broad spectrum of substrates. The type of materials processed will consist mainly of restaurant and market waste, expired food and canned goods from supermarkets, food industry waste, as well as non-contaminated slaughterhouse waste. This broad spectrum of wastes places high demands on materials processing systems: The plant has to be able to sort out lots of impurities (glass, and plastic packaging, cans, etc.) on the one hand; on the other hand, it has to grind up and homogenize various sized objects (pieces of meat, whole plant parts, fruits, etc.) and homogenize them for use in the bio-gas plant. Furthermore, liquid and slurry/liquid waste has to be fed into the plant via a dedicated line. Add to that strict hygiene guidelines that plants have to adhere to before they are authorised to process slaughterhouse waste, meat processing waste, or various types of waste that contains meat.
Figure 1 shows a schematic of the plant. The plant is divided into four main areas: A receiving bay with mechanical pre-processing, a thermal pre-treating area, a fermentation area with final storage and digestate output, as well as a gas collection system with upstream gas treatment.
For Hygiene reasons, the receiving bay where the mechanical processing takes place is in a closed, bird-proof, rodent-proof hall. The material arrives either on dump trucks or palletized and is dropped off in the receiving bay. From there, a spiral conveyor feeds the material into a screw mill. The screw mill performs the initial rough crushing, mainly to break open packaging. The material moves from the mill to the material sorter, where the organic fraction is placed in a suspension. Heavier materials are separated at this stage via a discharge chute in the base of the sorter. The suspension, which is still contaminated with non-fermentable light materials (mainly the remnants of plastic packaging and tubs), is conveyed to a sieve where the light materials are separated out, washed and pressed. The impurities are then transferred to a container and disposed of.
The cleaned suspension is fed through a temporary storage tank. Liquid waste, such as blood, arriving in tanker trucks is pumped into this temporary tank. From the temporary storage tank, the material moves to a hygienic treatment system. In the hygienic treatment system, pathogens are destroyed in a batch treatment process where the suspension is heated for an hour to a temperature of 70 °C. Finally, after a cooling stage where heat is recovered, the material arrives in the buffer tanks.
The substrate from the buffer tanks is then pumped into the two CSTR fermenters. The material ferments at temperature of 38 - 40 °C for 30 days, during which the organic substance is broken down and bio-gas is produced. Overflow from the CSTR fermenters flows into the post-fermentation fermenter, where final biological stabilization occurs. The post-fermentation fermenter is equipped with a dual-membrane cover and also serves as a gas storage vessel.
From the post-fermentation fermenter, the stabilized digestate is pumped into the final storage tanks, from which it is dispensed for use as agricultural fertilizer. The bio-gas is first fed into a biological washing system to remove hydrogen sulfide. Finally, the gas is cooled to remove any remaining water vapor, and is fed into the two cogeneration plants to produce electricity and heat. The electricity is fed through a transformer station into the intermediate-high-voltage grid. The heat is used primarily to cover on-site demand - especially in the hygienic purification plant. Excess heat can be distributed to nearby consumers if necessary. Excess gas, such as can accumulate during periods of maintenance on the cogeneration plants, will be incinerated with a gas flare. Once the plant is complete, it will be expanded in a second construction stage with the same capacity, and a third stage if necessary.
Author: Dr. Johann Chaloupka, Entec Biogas GmbH, Fussach (Austria)