Fine-tuning the fire: Plant controls improve waste incinerator economics
Thermal waste incineration plants are generally characterized by strong fluctuations in fuel characteristics, such as calorific value and water content. To keep emissions low, furnace controls have to meet stringent design, parameter and ease-of-use requirements. For large-scale furnaces, it makes sense to use model-based control systems, such as those commonly used for years in oil refineries. The result is a reduction in operating costs and lower quantities of flue gas.
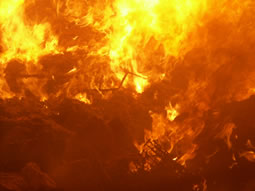
(01.06.2010) Predictive controller technology is based on the integration of a dynamic process model into the controller algorithm to achieve high performance, physical couplings and large time constants in the plants, all despite idle times. The speed with which the controller compensates for fluctuations in fuel, steam production upon load changes, as well as robustness and fault-resistance are significantly greater with high-quality model generation than they are in conventional controller systems using P, PI and PID controllers. The controller's "tuning" ensures a constantly high level of live steam production and outstanding emissions values under all operating conditions.
High fuel throughput is often critical in waste incineration plants. Because waste input in the combustion chambers cannot be measured, optimizing compensation for process malfunctions through the use of a well adapted model is critical in grate, rotary, and FICFB plants. Such optimization is the only way to achieve high waste throughput, while simultaneously ensuring low emissions.
The rapid and effective controller intervention necessary to control incineration is not possible using a traditional controller without a prediction model because, with traditional controllers, delays in the process can cause stability problems. The result is vibration or oscillation of the entire plant. A model-based controller can effectively avoid this problem. The graphic clearly illustrates that the boiler shown, controlled via fuel input, readjusts after only 30 seconds, despite no measured increase in the quantity of live steam. The readjustment compensates for both changes in target values and malfunctions without overcompensating.
Because power plant efficiency is increasingly becoming a competitiveness factor among plant suppliers and operators, we designed the controller from the bottom up to ensure that plants can be operated stably at the upper boiler and blast system limits with constantly high levels of steam production.
The forward-looking controller process discussed here also achieved a very high degree of fuel flexibility with respect to fluctuations in calorific and moisture content values. Optimal controller technology always uses every available adjustment unit to compensate for malfunctions caused by fuel, without the use of complicated parameter settings, with very rapid configuration times through intuitive weighting of controller and setting adjustment units. This technology makes adjusting a model-based controller significantly more straightforward than with PID-based systems.
The advantages of optimized controllers can be seen particularly in outstanding load sequence performance. For applications where heat-controlled operation is important, this system can be decisive in determining the economic success of a plant. Reducing the use of auxiliary burners and making buffer tank installation unnecessary reduces operating and investment costs.
Because rapid configuration times obviously have to be adhered to, all of the major plant types have been created in controller-ready designs and validated with process data. The following thermal plant types are currently available as pre-fabricated models and can be delivered with customer-specific plant data:
+ Grate firing plants for household-type waste
+ Stationary and circulating FICFB firing plants for a broad range of fuels * Biomass firing plants with grates and typical fluctuations in fuel quality
+ Rotary plants for hazardous waste, characterized by extremely irregular fuel input
A properly developed dynamic plant model includes the proper reinforcements, idle times, and time constants for fuel input, hydraulics, primary and secondary air systems, the recirculation gas system, and the boiler itself. Such a model typically makes it possible to calculate the live steam quantity, furnace temperature, and flue gas oxygen content 30 minutes in advance. However, because the fuel changes constantly, this prediction has to be updated at every sampling interval (approximately 1 to 10 seconds). This principle is known as a "sliding prediction horizon" and enables rapid adjustment of the plant controls, despite the changing influence of the fuel on combustion.
Controller systems with traditional PID controllers are only capable of reacting to discrepancies between target and actual values, depending on the process. However, this means that delays (idle times) in plant behavior necessarily cause very sluggish controller behavior, since compensating for malfunctions has to occur very slowly to prevent vibration. But this sluggish behavior is sometimes much too slow to prevent emissions. The controller structure, often consisting of a single loop, causes a further problem: namely, that a controller unit is often only assigned a single unit of adjustment. Decoupling the individual control loops is only possible by using complicated decoupling networks, but would be necessary due to the physical interdependencies between air, fuel, oxygen, emissions and steam production. Attempting the very complicated parameters settings for such override systems can lead to contradictory or confusing controller behaviors.
Model-based, predictive controls combine the effects of all of the adjustment units of the process values to be controlled into a global furnace controller. This ensures that the plant interactions mentioned above are fully taken into account and that, based on the prediction, the controller intervenes at the theoretically earliest possible moment. The result is stable, steady plant behavior.
Stable, rapid firing control prevents CO and NOx formation by inputting the correct amount of oxygen and optimizing temperature distribution in the furnace chamber. That, in turn, reduces operating costs (ammonia consumption) for secondary measures in DeNOx systems, such as SCR and SNCR. Furthermore, a high safety buffer from the CO limit value allows for an increase in plant efficiency by reducing residual oxygen content in gas emissions and a reduction in the amount of flue gas.
Author: Andreas Voigt, graduate engineer, Voigt+Wipp Engineers, Vienna (Austria)
www.voigt-wipp.atFoto: M. Boeckh